Porosity in Welding: Identifying Common Issues and Implementing Best Practices for Avoidance
Porosity in welding is a prevalent problem that typically goes unnoticed till it creates considerable problems with the honesty of welds. This usual flaw can compromise the toughness and durability of bonded structures, posing safety and security dangers and resulting in pricey rework. By comprehending the origin of porosity and carrying out effective avoidance techniques, welders can considerably improve the top quality and integrity of their welds. In this discussion, we will certainly check out the key aspects adding to porosity development, examine its destructive effects on weld efficiency, and go over the finest practices that can be adopted to reduce porosity incident in welding processes.
Common Reasons of Porosity

One more regular wrongdoer behind porosity is the presence of contaminants on the surface of the base metal, such as oil, oil, or corrosion. When these impurities are not properly gotten rid of prior to welding, they can evaporate and end up being trapped in the weld, causing flaws. Making use of filthy or wet filler materials can present pollutants into the weld, contributing to porosity concerns. To minimize these typical sources of porosity, comprehensive cleansing of base steels, appropriate shielding gas option, and adherence to ideal welding specifications are important techniques in accomplishing premium, porosity-free welds.
Influence of Porosity on Weld Top Quality

The presence of porosity in welding can dramatically compromise the architectural integrity and mechanical properties of bonded joints. Porosity creates spaces within the weld steel, compromising its overall strength and load-bearing capacity. These voids function as stress focus factors, making the weld more prone to fracturing and failure under applied lots. Additionally, porosity can minimize the weld's resistance to deterioration and other environmental aspects, even more diminishing its durability and efficiency.
One of the key effects of porosity is a decrease in the weld's ductility and strength. Welds with high porosity degrees often tend to display reduced influence stamina and lowered capacity to deform plastically prior to fracturing. This can be particularly concerning in applications where the bonded elements are subjected to vibrant or cyclic loading problems. Furthermore, porosity can hinder the weld's ability to successfully transmit pressures, causing premature weld failing and prospective security dangers in critical structures.
Ideal Practices for Porosity Prevention
To boost the structural stability and top quality of bonded joints, what details measures can be executed to lessen the event of porosity during the welding process? Making use of the proper welding technique for the specific material being welded, such as adjusting the welding angle and gun position, can even more stop porosity. Routine assessment of welds and prompt remediation of any type of issues determined throughout the welding process are important methods to avoid porosity and create premium welds.
Value of Appropriate Welding Techniques
Implementing appropriate welding methods is critical in making sure the structural integrity and quality of bonded joints, building on the structure of efficient porosity prevention measures. Welding strategies straight affect the overall stamina and longevity of the bonded structure. One key element of appropriate welding methods is maintaining the proper warm input. Extreme heat can bring about boosted porosity because of the entrapment of gases in the weblink weld pool. Conversely, insufficient warm may result in incomplete combination, developing possible weak points in the joint. In addition, making use of the appropriate welding parameters, such as voltage, existing, and take a trip speed, is vital for attaining sound welds with very little porosity.
Moreover, the choice of welding procedure, whether it be MIG, TIG, or stick welding, must line up with the specific demands of find more information the task to ensure ideal outcomes. Correct cleaning and preparation of the base steel, along with selecting the best filler product, are likewise vital components of efficient welding strategies. By adhering to these finest methods, welders can decrease the risk of porosity formation and produce top notch, structurally audio welds.
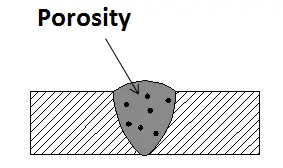
Testing and Quality Control Actions
Testing treatments are essential to detect and prevent porosity in welding, ensuring the toughness and longevity of the last item. Non-destructive testing methods such as ultrasonic testing, radiographic screening, and aesthetic assessment are typically employed to identify potential issues like porosity.
Conducting pre-weld and post-weld examinations is likewise crucial in keeping high quality control standards. Pre-weld examinations include verifying the materials, equipment setups, and tidiness of the workspace to stop contamination. Post-weld evaluations, on the various other hand, examine the last weld for any type view it now of issues, including porosity, and validate that it meets defined standards. Carrying out a comprehensive top quality control plan that consists of thorough screening procedures and assessments is paramount to minimizing porosity issues and guaranteeing the total quality of welded joints.
Conclusion
Finally, porosity in welding can be a typical concern that affects the high quality of welds. By recognizing the usual reasons of porosity and implementing best practices for prevention, such as proper welding methods and screening measures, welders can make certain excellent quality and trustworthy welds. It is necessary to focus on avoidance techniques to lessen the incident of porosity and preserve the stability of welded structures.